OSHA Construction Industry Requirements for PPE by a Certified Safety Professional
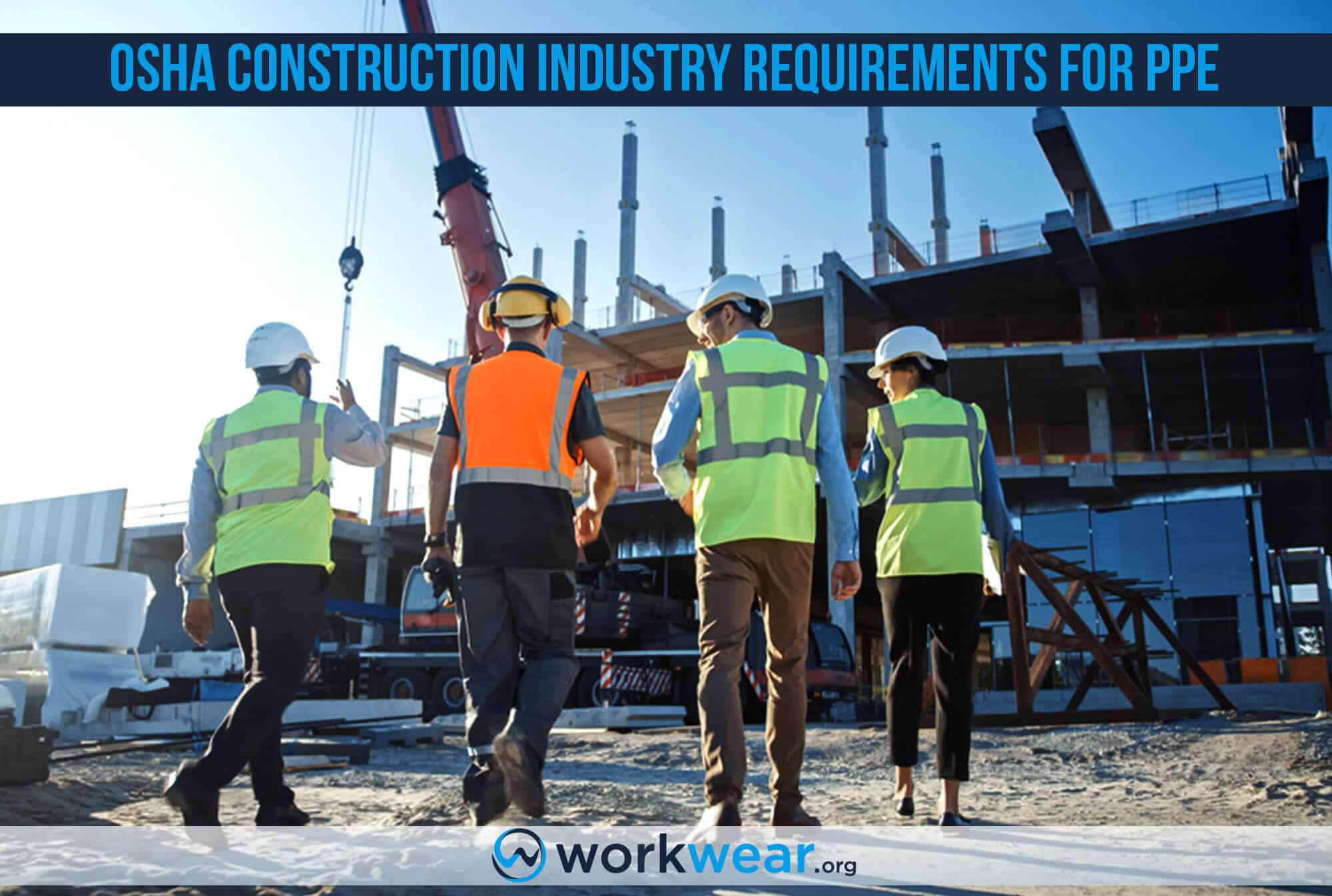
Personal protective equipment, or PPE for short, is an important defense against the various hazards you can encounter in the workplace. PPE is considered the last line of defense in protecting against workplace hazards. The construction industry relies on them as the nature of the work can make higher-tier controls, such as elimination, substitution, and engineering, difficult, if not impossible, to utilize. Think of it this way. There are reasons why the rules are often different in the OSHA construction standards compared to the general industry.
For instance, if you are constructing a new item or making a major repair using hot work, you must use PPE. Why? Because you are holding a welding lead or torch that is right in front of you. And the temperatures are hot enough to melt metal. Think about that for just a moment or two. The tool used for the repair or alteration is hot enough to melt metal! And you are holding it right in front of you. So you better believe you’ll need to use your PPE well. With all of that said, let’s look at the general requirements the Occupational Safety and Health Administration (OSHA) has to say about PPE in construction. You can find the requirements here if you want to look for yourself. Look in 1926 Subpart E for “Personal Protective and Live Saving Equipment.”
General Criteria
Keep PPE Reliable and Sanitary
To start with, PPE is required to be kept in a sanitary and reliable condition. This doesn’t surprise you. There are many different forms of PPE that serve many different functions. First, let’s look at the need for reliability. From an earlier example, if you are welding or cutting, you’d want PPE that keeps the molten slag and sparks off you. Wouldn’t that require your PPE, whether gloves, a face shield, or a welding jacket, to be intact? If there are significant or worse holes in them, you may be in a world of hurt.
You’d also want your PPE to be intact for other hazards. For example, if you work with chemicals that can burn you, you want the right glove. Even if the gloves or other PPE are in good condition, if they aren’t rated for the type of chemical… you’ll probably need a medical professional. So don’t skimp on checking that your PPE is suitable for the job you’re engaged in.
Now PPE also needs to be kept sanitary. Respiratory protection presents an item of particular need in this regard. Bacteria and other microorganisms can grow in the environment. The breathing zone is warm, moist, and dark. After all, there’s no light in there, and your breath is warm and moist. If you don’t clean and sanitize it, it could make you sick on the next use. So it should make a lot of sense to ensure that your PPE is kept clean and sanitary.
Employee-Owned Equipment
In cases where employees are utilizing their PPE, the employer doesn’t have to worry about it. Right? Nope. That couldn’t be further from the truth. Just because employees bring their own PPE doesn’t mean the employer has no responsibilities.
On the contrary, employers must ensure the adequacy of the PPE and ensure it is maintained in a reliable and sanitary condition. The work requires what it requires. Employers control how the work is done. Failure to address this can lead to injuries that hurt people and diminished production. So check on employees’ PPE and ensure it’s getting the attention it needs to function properly.
PPE Design
Does OSHA require employers to design their protective equipment? If so, that can seem like a bit much. Most employers are outside the business of designing PPE. Thankfully, employers are not required to design their PPE. There are consensus standards, such as from the American National Standards Institute (ANSI); OSHA accepts the general design, performances, and testing of the various types of PPE. We’ll get into the specifics when looking at specific PPE types. What is the general design requirement? Well, it’s pretty simple. All PPE must be of a safe design and construction suitable to the specific work and hazards.
So, Who’s Required to Pay for PPE?
For some, this is the real reason they’re reading this. Who has to pay for all this? Just kidding. But it’s a valid question. Who is responsible for paying for the required PPE for a given job type or worksite? Well, according to OSHA, employers drew the short straw. The required PPE must be provided at no cost to the employee. But that isn’t the whole of it. Oh, No. There are some exceptions to this. So, here they are:
- If you have non-specialty safety-toed work shoes and can wear them off the job site, I’ve got news for you. The employer doesn’t have to pay for them.
- If the employer provides metatarsal protectors, but an employer wants work boots with built-in metatarsal protection, the employer doesn’t have to pay for those boots.
- The employer doesn’t have to pay for clothing, creams, ointments, or other gear meant to help protect against weather conditions.
- If an employee purposefully damages or loses their PPE, the employer doesn’t have to pay for it.
- If employees provide their own adequate PPE and are not required by the employer, the employer doesn’t have to replace the employee’s PPE.
There are several situations where employers don’t have to pay. However, if they don’t, and an employee is allowed to perform work without the required PPE, it can be a bad day for both the employer and the employee. While OSHA does allow situations where employers don’t have to pay for PPE, they must remember that if employees are to do the job, they must have what they need to do it safely and effectively. This is true regardless of who is responsible for purchasing, evaluating, and maintaining PPE.
On to Specific PPE Requirements for Construction work
Now’s the part where we can look at what’s required for some common PPE you’ll need to perform construction work. They will include head protection, eye protection, hearing protection, foot protection, and respiratory protection.
Head Protection
If you’ve got a potential danger of falling objects impacting the head or there is a risk of bumping your head at the worksite, you’ll need a protective helmet. This is commonly called a hard hat. OSHA considers three consensus standards acceptable for protective helmets to meet. There are as follows:
- American National Standards Institute (ANSI) Z89.1-2009, “American National Standard for Industrial Head Protection”
- American National Standards Institute (ANSI) Z89.1-2003, “American National Standard for Industrial Head Protection”
- American National Standards Institute (ANSI) Z89.1-1997, “American National Standard for Industrial Head Protection”
All three of these are incorporated by reference in OSHA 1926.6. That said, if the employer can demonstrate that the hard hats they choose are just as protective (or better) than those that meet the listed standards, they can use them. This is a way that OSHA allows newer consensus standards to be used in selecting this type of PPE. If there is exposure to electrical hazards, the hard hats must also meet the electrical insulation standards of any of the consensus standards listed above.
Hearing Protection
If you’ve got a noisy environment, hearing protection will probably be in your future. Hearing protection is required when you have noise levels greater than those allowed in the construction noise standard, and you can’t engineer the noise lower than the permissible exposure level. In addition, OSHA requires that ear protective devices need a competent person to fit them or determine which ones will suit the work area.
I want to take a moment to note that it is important to use hearing protectors correctly. Foam earplugs come to mind. In the case of foam earplugs, many of them need to be rolled up between the fingers. Then, they are inserted while holding the top of your ear with the other hand. They are allowed to unroll and expand. This fills up your ear and offers significant protection when done correctly.
Respiratory Protection
Some construction worksites can have many different breathing hazards from dust, fumes, gases, and vapors. Sometimes, those hazards are created by doing work such as demolition and welding. Even painting with aerosols can present a breathing hazard in the work area. That’s why respiratory protection, in the form of respirators, is needed. Interestingly, the OSHA construction standard for respiratory protection refers to the general industry’s standards. It says that the requirements for respiratory protection applicable to construction are the same as what’s laid out in OSHA’s 1910.134 standards. So, for your information, when you see 1910, it’s for the general industry. When you see 1926, we’re talking about the construction industry.
This standard is fairly detailed on how to handle respirators in the workplace. Let’s break things down to their major points.
- To start off with, there is a requirement for employers to develop a written respiratory protection program. That program will cover topics including, but not limited to:
- Respirator selection procedures
- Medical evaluations for employees required to use respirators.
- Fit-testing procedures for tight fitting respirators.
- Procedures for proper use of respirators
- Procedures relating to the proper maintenance and discarding of respirators
- In cases where the employer has found that respiratory protection is not needed but is voluntarily requested by employees, this may be permitted under the following conditions:
- The employer must determine the respirator is not causing a hazard itself.
- The employer must take the portions of the written respiratory protection program such that employees using respirators voluntarily are medically cleared to use and maintain them.
- This doesn’t generally apply to filtering face pieces, otherwise known as dust masks.
- The employer must provide training to employees to accomplish the requirements of their respiratory protection program.
- When selecting respiratory protection, employers must select National Institute for Safety and Health (NIOSH) approved respirators.
- The respirators must be used per the requirements of their certification.
- Employers have to identify and evaluate the respiratory hazard present in their workplace.
- To know exact numbers, often industrial hygiene surveys will be needed.
- You can get an idea of what hazards may be present just by looking at the labels and safety data sheets for the materials used in the work site. Spray paint is an example of this.
Eye Protection
If you have hazards to the face and eyes from various workplace sources, you will need to protect yourself and your employees. There can be many hazards, such as flying particles and debris, molten metals, and chemical splash hazards, to name a few. A major thing needed for eye protection is that it offers protection from the side. OSHA allows for detachable side shields to be used on safety glasses. But there are lots of other considerations under the standard. Let’s take a look at them.
- If employees use prescription glasses, they either have rated eye protection that incorporates their prescription or must wear safety eye protection over their prescription glasses.
- They have to provide suitable protection against the hazards faced. If you use impact safety glasses against splash or fine dust hazards, your eyes might need to improve.
- They need to be reasonably comfortable. They certainly shouldn’t create a hazard in and of themselves.
- They need to fit snuggly and not hinder the normal movements of the wearer.
- They need to be durable.
- They need to allow for cleaning and disinfection.
- They need to meet one of the following consensus standards:
- ANSI/ISEA Z87.1-2010, Occupational and Educational Personal Eye and Face Protection Devices
- ANSI/ISEA Z87.1-2003, Occupational and Educational Personal Eye and Face Protection Devices
- ANSI Z87.1-1989 (R-1998), Practice for Occupational and Educational Eye and Face Protection
Foot Protection
Foot protection sometimes needs to be on a whole other level regarding protection for the construction industry. It’s not to say that you will never see some of the hazards in construction in other industries. But it’s common when demolition or building structures to have materials like embedded nails in them. There are many general industries, like warehouses, where you would rarely, if ever, risk puncturing your foot because of an errant protruding nail. You can’t say that in the construction industry. Specifically, I think of carpentry and similar levels of construction work for certain hazard types.
So, while protective footwear must meet the same consensus standard, the American National Standard for Men’s Safety-Toe Footwear, Z41.1-1967, specific protection levels should vary with the specific worksite hazards. An assessment is needed to ensure the right foot protection is chosen for the job. Nobody’s shocked at that.
Key Takeaways
We’ve covered a lot concerning the OSHA construction standard requirements for PPE. But do you believe that there’s a fair bit more that could be dug into? Well, let’s not dwell on that for now. So, let’s get into the key things you should remember from this article.
- The PPE Requirements for Construction work entail head protection, foot protection, hearing protection, respiratory protection, and eye protection
- With some exceptions, employers are responsible for evaluating the PPE needed, providing it, and paying for it.
- PPE, whatever the type, needs to be constructed such that it’s suitable to protect against the hazards it’s being provided for.
- Employers must still check employee-provided PPE for adequacy and ensure the maintenance and correct use.
- Generally, PPE needs to meet some standard, such as with ANSI or NIOSH.
- The referenced standards may be outdated, but in most cases, if you can demonstrate the PPE is at least as protective as what’s detailed in the referenced standards, such as with a newer standard, you can use that PPE.
- If PPE isn’t kept in a reliable, maintained condition, it may not be suitable for the work.