OSHA Requirements for Work Boots – From a Certified Safety Professional
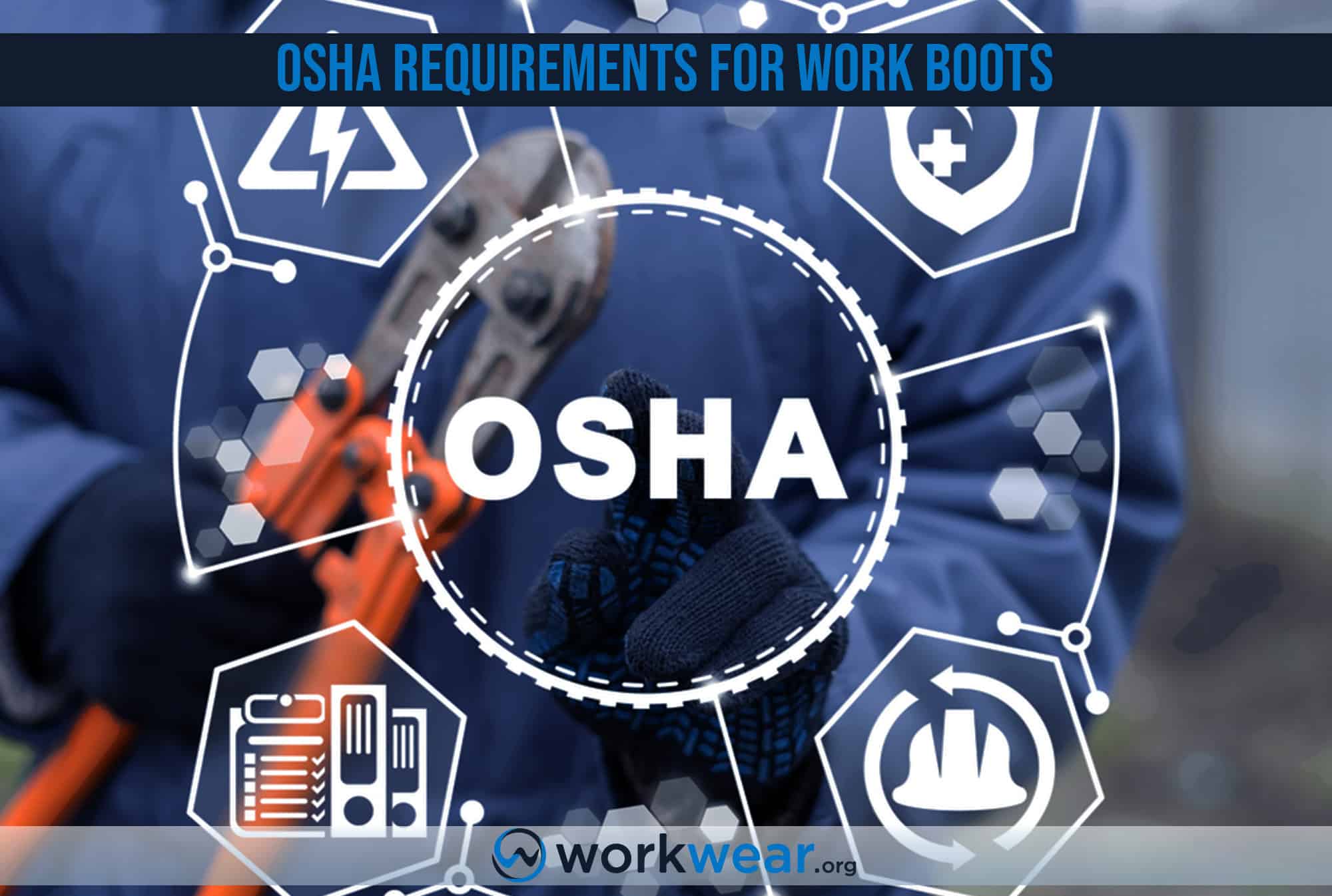
Safety work boots are an important part of maintaining good safety and efficient work at your job. But how do you know what makes good, safe work boots? Does anyone have insight on this? The answer is simple, the Occupational Safety and Health Administration does. So, what are the requirements for work boots? As is often the case in life, it depends. What’s your work environment like? What materials do you work with? Do you change major job tasks often? All these questions and more must be answered before you know the requirements. So, how about we dive in!
OSHA Requirements for Work Boots and PPE Compliance
As is the case with many things, the specific requirements OSHA has for work boots depend on the actual hazards present in the workplace. So, how can you know if OSHA needs to tell you the specifics? Under the PPE Standard (1910.132), they require employers to do a hazard assessment. This is for more than just the type of work boots employees may need. No, this includes a look at all of the workplace hazards for the area or job being looked at so that any potential personal protective equipment can be identified and provided.
The hazard assessment will involve looking at the operation and identifying and anticipating the hazards that could be reasonably encountered.
The hazards that can be encountered will differ from workplace to workplace. For instance, if you work in a warehouse where the racks are designed such that it’s practically impossible for any items to fall on employees’ feet, you could provide sturdy work boots. But, on the other hand, if you work in an industrial manufacturing facility with potential electrical, falling material, and puncture hazards, you will need much more protective shoes.
It’s worth noting that there is a provision in OSHA for employee-supplied personal protective equipment. Employees are allowed to do this in the standard. However, that same standard puts the responsibility on the employer to ensure that the PPE is adequate. This will include making sure proper maintenance and sanitation are performed.
It’s usually in the employer’s best interest to provide what’s needed and ensure that said PPE, such as work boots, is maintained and taken care of.
It’s a lot easier to manage what you know you have provided rather than be on the lookout for all sorts of variations on the types of work boots an employer provides. It’s no fun trying to track everything down for compliance.
As is the case with most things in safety compliance, you need to document the hazard assessment. The assessment needs to include all the following information:
- The work area was evaluated.
- The person who is certifying that the hazard assessment took place.
- The date the assessment took place.
- Clear identification of the document certification.
You could achieve this part and identify the person doing the certification by stating something to this effect: “This PPE hazard assessment has been performed and certified by …”
Choosing Safe Work Boots
Identification of hazards is necessary and good. But if you leave things there, you still need to take care of the issues. Identifying hazards is like having an exterminator open a wall to expose a bug infestation… and then leaving without doing anything else. That doesn’t seem very useful. Further, if no further action is planned, you have a significant hole in your wall. The exposed bugs will probably avoid light and set up shop somewhere else.
So, when you have figured out what hazards are facing employees’ feet, you need to find shoes that will offer protection against those hazards. Many different protections can be in work boots. To keep things simple, we’ll look at some types of protection the boots can have.
Safety toe
This will be needed if you have the risk of falling materials or tools to the toe region of the feet. They come in steel and composite toe varieties.
Metatarsal guard
These protect higher up on foot. The guard itself is named for the part of the foot it protects. These can be internal or external. Some common hazards to this foot region can come from doing hot work-related jobs such as welding or cutting. It’s common for maintenance personnel to need extra foot protection in this way.
Chemical or oil-resistant sole
If your workplace is industrial, there’s a good chance you might encounter chemical residues that can prematurely wear out your boots if given a chance. It would help if you had a boot that resists such ill effects.
Puncture resistant sole
You’ll need such a sole, which can be through the sole itself or an insert if you work in an environment where you might come across sharp protruding metal or similar materials.
Heat Resistant
Expect to find this on maintenance staff that engages in hot work. The boots must tolerate the very high temperatures encountered from such work.
Electrical Hazard Rated
The boots with this type of rating are made to resist electrical hazards that might be encountered. You can expect certain maintenance employees and electrical staff to need such protection. Additionally, suppose the work area itself is conductive and near electrical equipment. In that case, these boots can be a way to prevent any potential issues with electrical energy reaching employees through their feet.
Though we’ve covered many protective features that a work boot may need, this is a partial list. The specific protection your work boots need will depend on the hazards present in your workplace. In some cases, having a general duty boot that protects the common hazards, most employees face in the workplace can make sense. But keep the general duty boots from serving in place of specialty boots and shoes more geared towards the specific job duties. Some jobs are different enough that general-duty boots just won’t cut it.
Once you’ve selected the work boots or boots needed to address the hazards, you must communicate this to the affected employees. After that, you’ll need to offer a selection of boots that protect against hazards and fit the employees. Many employees routinely work eight or more hours a day, and that’s how long they will be in their work boots. So, they need to fit and be as comfortable as you reasonably can get them.
This should go without saying, but it can happen in the workplace more often than it should. You aren’t to use damaged or defective boots. Yes, that is an actual OSHA requirement. And if you think about it, it makes sense. If the boot is damaged, at least to a significant degree, it can’t function to the degree it should. So, those who wear their boots until it’s a weird Frankenstein’s monster of their former self, you’ll need to quit doing that. Employers will need to make sure employees replace damaged or defective boots.
Work Boot Training
Did you think you could give employees a voucher for their boots, and you were good to go? Well, sadly, it’s not quite so easy. Just because you have identified the hazards and selected the right boots for the job doesn’t mean things stop there. There are several things that OSHA requires employers to train their employees on. Here’s the list, so buckle up! Nah, it’s not that bad. And it should make sense.
- It would help if you informed employees when they need to wear their work boots as well as what work boots to where when they need to. General duty boots work out fine, depending on the job task or job area. But that will only work if you trod around in the muck and mire.
- You must show employees how to properly put on, take off, adjust, and wear their work boots. Your employees should have a good idea if they are similar to regular shoes and boots.
- It’s vitally important that employees understand the limitations of their work boots. Sure, work boots might be good against relatively small, falling materials. They may take the substantial weight. But at some point, they won’t protect your feet. For instance, if a 300-pound product falls from a significant height on your boots, they will likely offer little protection. Think of it this way. It’s far better to avoid getting hit in a sport than to find out how effective your padding is.
- You must teach your employees how to care for and maintain their work boots. Additionally, they need to know their useful life and how to dispose of them properly. The useful life and disposal part will largely depend on how they are being used. The harsher the environment they are used in, the shorter the useful life of the boot likely will be. If you clean them frequently, removing potentially harmful materials and chemicals, you might be surprised at the life you can get out of your boots.
There’s a fair bit to cover, but it should make sense. Once you’ve done the training, you get to do the fun task of verifying their understanding and competence. You only know that any of the training taken if your employees show you they both know a can do what you trained on. It’s better to know if there are problems early so you can fix them before they get any bigger.
If you need to change the type of work boots used for the various areas you have in your workplace, you will need to do retraining on the changes. Further, if employees demonstrate that the training didn’t take, whether soon after the training or later, they will need to go through retraining. Evaluate your training to ensure that it’s effective. Retraining will only work if the training itself is the problem.
So, Who Pays for the Boots?
In most cases, the employer is required to pay for the work boots. This is the case with all forms of personal protective equipment. There are some exceptions to this, however. So, let’s look at them.
- Non-specialty protective toe work boots and shoes, and non-specialty prescription safety eyewear doesn’t have to be covered by an employer. The catch is that this is true only if they allow the footwear and eyewear to be worn off the job site.
- If an employer provides metatarsal guards, employees request to wear built-in metatarsal guards in their footwear, which the employer allows. The employer doesn’t have to pay or reimburse the employees who take this option.
- The logging boots required by the 29 CFR 1910.266(d)(1)(v) standard don’t have to be paid for by the employer.
- Regular street clothes, shoes, and work boots don’t have to be paid for by the employer.
- Items, including clothing, creams, and equipment used for protection from the weather, don’t have to be paid for by the employer.
- If employees ask to use compliant, adequate PPE that’s different from what the employer provides, the employer can allow this. They won’t be required to pay for such PPE or replacement PPE.
- An employer does have to pay for replacement personal protective equipment, such as work boots. There is an exception, of course. If an employee has lost or deliberately damaged the boots, the employer is not obligated to replace them.
It can get tricky to not replace damaged work boots or PPE in general based on employees losing them. However, they can safely perform the work if they have the required boots. After all, you required and paid for the boots for a reason as an employer.
Work Boot Construction and Performance
I didn’t think any old boots made by any random manufacturer would do. Well, OSHA requires footwear to meet one of 3 consensus standard sets. They are as follows:
- ASTM F-2412-2005, “Standard Test Methods for Foot Protection,” and ASTM F-2413-2005, “Standard Specification for Performance Requirements for Protective Footwear”
- ANSI Z41-1999, “American National Standard for Personal Protection — Protective Footwear”
- ANSI Z41-1991, “American National Standard for Personal Protection — Protective Footwear”
Each of these is an OSHA 1910.136 Personal Protective Equipment Foot Protection Standard due to their incorporated by reference in 1910.6. So, they are regulations now! That said, there is one other allowance to meet the construction and performance requirements OSHA has. See, they allow employers to demonstrate that the protective footwear they select is as least as good and protective as those that meet one of the above consensus standards. That’s not necessarily easy, but it is an option if you can have your boots designed and tested outside of those standards.
You may have yet another thing to buy in the form of one of those standards. Unfortunately, they tend not to be free. But, in most cases, you shouldn’t need to worry about that. Safety footwear manufacturers usually mark their work boots for the standards they meet. This includes specific protections such as metatarsal guards, safety toes, and electrical hazard ratings. So, you select a vendor, search for shoes meeting your requirements, and check to ensure they are marked or have a specification sheet showing that they meet an applicable standard. To this end, employers can use updated versions of the standards referenced. OSHA discussed this in their 2009 final rule detailing updating safety standards referencing outdated consensus standards. Generally, the newer standards are equal to or better than the outdated ones. This allows for using improved technology in safety footwear such that safety standards remain high for your workplace.
Conclusion and Key Takeaways
We’ve reached the end and have covered a lot. So much that remembering it all may be confusing. Let’s boil things down to the essentials.
- A hazard assessment must be performed for the various job tasks and areas. This tells you what the work boot needs to protect against.
- Select the right work boots for the hazards faced. Inform employees of what’s required and when.
- Train employees on properly using, caring for, and maintaining them. They also need to know how to wear them and their limitations properly.
- Employers generally have to pay for the work boots. But there are some exceptions, such as non-specialty boots allowed to be worn off-site.
- There are consensus standards, such as through ANSI and ASTM, that boots must meet to be considered compliant. Or you could try to go another route if you can demonstrate the boots made are just as good (or better) as those made via the standards mentioned above.