Personal Protective Equipment – Statistics, Facts & Insights
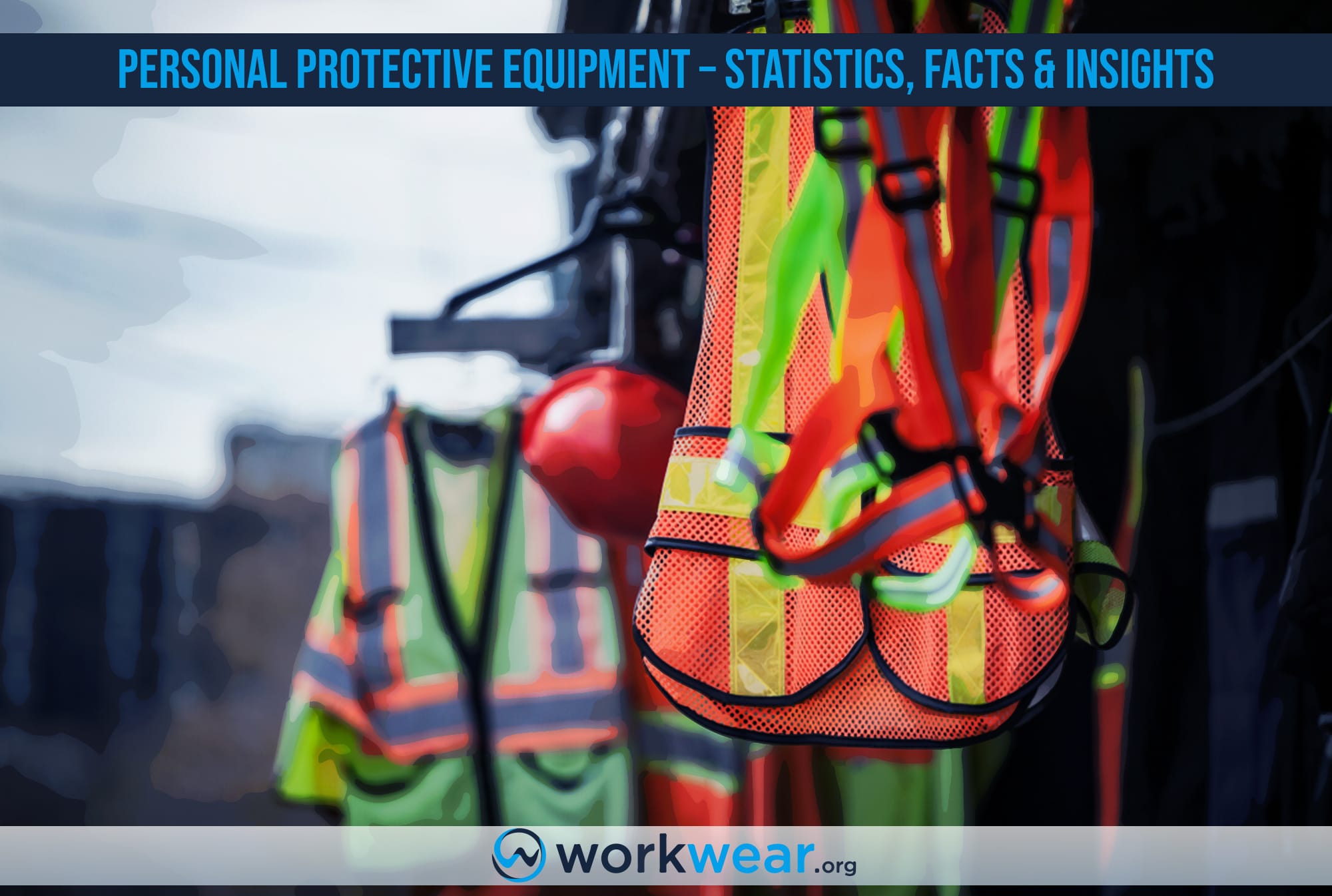
NIOSH (National Institute for Occupational Safety & Health) defines PPE as the technical methods, processes, techniques, tools, and materials that prevent work-related accidents, injury, illness, and death. According to WHO, the purpose of these materials is to minimize exposure to hazards such as biological, radiological, electrical, chemical, mechanical, and others. Construction, chemical, mining, and pharmaceutical workers require regular protection from hazards.
According to WHO & ILO, 2 million people die each year due to work-related causalities (1).
In this article, we will analyze the importance of PPE in every industrial sector and the disadvantages of not using proper PPE.
Statistics to Show the Importance of PPE
Construction
The construction sector is considered one of the most dangerous fields to work in. According to the U.S. Bureau of labor statistics, the construction industry accounted for 46.1% of all fatal falls, slips, and trips in 2019 and 2020 (2). When manufacturing, work practice, and administrative controls are not in control, and employers do not provide PPE, then employees expose to work-related injuries and fatalities.
On average, 15 deaths per day are recorded in the construction industry (3).
However, these work-related injuries can be controlled via PPE. Standard PPE tools construction workers require include safety helmets, eye & ear protectors, mark & respirators, protective gloves & clothing, and safety belts & footwear. Proper use of PPE at construction sites is also mandatory, as it can prevent 37.6% of occupational injuries and diseases, OSHA (4). For instance,
- Workers can develop hearing loss without earplugs and ear muffs at construction sites.
- Lack of hard hat protection can lead to head injuries.
- Without protective gloves, manufacturing, and construction workers can experience lacerations to the hands and fingers.
Mining
Like construction job sites, the mining industry is also a hazardous workplace. Mining hazards include ground or strata failure, the inrush of chemicals, inundation of any substance, winding operations, mine shafts, gas outbursts, airborne contaminants, and spontaneous combustion. MSHA reported 2,705 chemical-related injury and illness cases due to contact with acids/alkalis in the mining sector (5). All of these cases were caused due to lack of PPE requirements, safety culture, and training methods. The chemical-resistant glasses, gloves, face shields, respirators, and footwear are standard PPE that should be used in the mining sector to reduce high-risk activities.
Pharmaceutical
U.S. Bureau of Labor Statistics recorded 1.6 nonfatal occupational injuries per 100 full-time workers in the pharmaceutical manufacturing field in 2020 (6). Pharmaceutical manufacturing facilities contain combustible and flammable materials, causing uncontrolled fires, burns, and smoke inhalation. Many chemicals are also used during primary and secondary processing, which, if accidentally ingested or inhaled, can become hazardous to human health. To fight against UV rays, carbon monoxide exposure, and biological hazards, recommended PPE includes protective apparel like gowns & coveralls, gloves, shoe covers, face masks, goggles, N95 respirators, and PAPR (powered air-purifying respirators).
Ultraviolet radiation in the range of 295-325nm induces opacities in the eye’s lens photochemically, whereas cataracts are caused by radiation above 315nm (7).
1. Types of PPE
Choosing the correct type of PPE depends on the industrial needs and requirements. The table below shows the PPE types as per body parts (8)
Body Parts |
PPE |
Protects from following Hazards |
---|---|---|
Eyes |
Goggles, face screens, visors, safety spectacles, visors |
Metal splash, radiation, chemical vapors, dust, projectiles, temperature variations |
Head & Neck |
Hairnets, bump caps and safety helmets |
Falling or slipping of objects, head-banging risks, extreme temperatures, chemical drips, hair getting tangled in industrial equipment |
Ears |
Earplugs, earmuffs or defenders and canal caps |
Exposure to high intensity of sound levels |
Hands and arms |
Gauntlets, inner cotton gloves with cuff |
Cuts, radiations, electric shock, abrasion, biological acids/alkalis |
Feet & legs |
Protective toecaps, foundry boots, chainsaw boots, wellington boots, penetration-resistant safety boots |
Falling machines, electrostatic build-up, heavy loads, metal drips, heavy loads |
Lungs |
Respiratory protective equipment (RPE) |
Oxygen-deficient workplace, chemicals, vapors, bags of dust or gases. |
Complete body |
Chemical suits, boiler suits, life jackets, conventional or disposal overalls, aprons, safety ropes |
Dust, chemical, falling objects, spray guns, penetration |
2.Effects of using Improper PPE
If the employers fail to provide high-quality PPE to employees or if the employees don’t wear PPE, they could become a victim of severe injuries and fatalities. Although it is essential to wear PPE, many workers choose not to wear it and completely ignore the training and workshops on PPE. In 2005, a training program conducted by the Environmental Health & Safety department of NYU reported the following statistics (9):
- Hard hats were only worn by 16% of workers who had head injuries.
- Seven hundred seventy workers faced injuries, and only 1% of these workers were using face protection.
- Safety shoes or boots were only worn by 23% of workers suffering from foot injuries.
- Eye protective equipment was worn by only 40% of the workers with eye injuries.
These statistics depict that workers do not wear PPE because they don’t know enough about safety and protection during working hours. Employers, therefore, are required to train all the workers, and these workers must know the answer to the following questions (10):
- When is it necessary to wear PPE?
- What type of PPE is necessary?
- Why is it essential to know the limitations of PPE?
- How to properly wear, adjust and take off PPE?
- When should PPE require proper care, maintenance, and disposal?
3. PPE Management Plan
The modules of the PPE program depend on the type of industry, though it should comply with the OSHA standards:
Hazard Assessment
U.S. Bureau of Labor Statistics reported that most workplace injuries, illnesses, and fatalities are caused when sectors don’t identify or recognize hazards. It is essential to:
1. Collect and review data about the hazards likely to be available in the workplace.
2. Perform initial and periodic workplace inspections of the job site to unveil new hazards.
3. Examine injuries, fatalities, illness, incidents, and past events or accidents.
4. Filter hazards that may cause emergencies.
5. Analyze the severity and probability of events that could cause hazardous situations.
PPE Selection & Use
Once employers assess hazards, the second step involves PPE selection and usage. While selecting PPE, employers should choose comfortable tools, equipment, and appropriate items. This will encourage employees to wear PPE feasibly. Besides, if an employee requires several items to be worn together, their size and compatibility should be checked properly. If PPE equipment and items don’t fit properly or show compatibility, the purpose of providing safety and protection won’t be achieved. Lastly, the selected PPE should follow OSHA and ANSI requirements.
Inspection and Amendment of worn-out PPE
Another crucial step of PPE is to inspect worn-out PPE. Each PPE should be inspected before and after every use. Damaged PPE should be repaired or replaced as needed. For instance, if your employees require a hard hat, employers should look for cracked, missing straps and torn and frayed pieces. It is the responsibility of the employee to report damaged equipment to senior management.
Employee Training
As described earlier, most incidents and accidents occur due to the negligence of humans or human error. This can be prevented through proper guidance and training. The employer must document the training program and prepare a certification for each training module. These training programs must include what type of protection is needed for each body part.
Continuous Monitoring
Once trained, continuous monitoring of the PPE program should be performed at regular intervals to amend or update PPE requirements. Monitoring the PPE program also ensures its ongoing effectiveness in the workplace.
Conclusion
Personal Protective Equipment (PPE) is safety gear designed to protect workers in the workplace from potential hazards. It includes masks, gloves, goggles, hard hats, and other protective clothing. PPE can be used in various settings, such as construction sites, manufacturing plants, and medical facilities. PPE has been proven to reduce the risk of injuries and illnesses in the workplace. In addition to protecting workers from potential hazards, PPE helps employers meet their legal obligations to provide a safe working environment for their employees. With the proper selection of PPE products, employers can ensure that their workers are protected from potential harm while on the job.
References
1. World Health Organization (2023), WHO/ILO: Almost 2 million people die from work-related causes each year, URL: https://www.who.int/news/item/16-09-2021-who-ilo-almost-2-million-people-die-from-work-related-causes-each-year
2. US Bureau of Labor Statistics, (2022), A look at falls, slips, and trips in the construction industry, URL: https://www.bls.gov/opub/ted/2022/a-look-at-falls-slips-and-trips-in-the-construction-industry.htm